From Coil to Coil
Slitting lines

Steel Slitting Lines
Metal sheets or strips suppliers always need slitting machine and cut to length machine line for the production of metal sheets with different widths or lengths from GI (galvanised iron), PPGI - PPGL (pre-painted galvanised iron), PCI (pre-coated steel) or stainless coils in large quantities.
A steel mill most of time produces only wide steel coils, and steel or metal fabricators always use a slitting and cut to length machine line to manufacture steel strips with different widths or metal sheets with fixed lengths. A metal slitting machine line has been designed to cut longitudinally the wide steel coils into different narrow steel strips for continuously producing cold formed sectional steel products.
Basically there are two types: high-speed and normal-speed slitting machine line. A High-speed slitter can works at max speed over 150 m/minute and over 10 strips can be produced; while a normal-speed slitting machine can work at most 40m/min with less than 10 strips slit.
Sheet metal coil slitting lines production.
Everything from highway rails, to HVAC components, to automotive components and possibly some of our kitchen appliances were produced using sheet metal coil slitting lines, cut to length lines, or punch press lines.

Slitting lines
We supply slitting lines, able to satisfy the needs of different types of customers
High performance lines and great flexibility for coils up to 45 tons and a work speed up to 400 m/min, suitable for steel mills, service centres, the automotive sector and many others. Compact, simpler and very flexible lines, in cases where a lower production capacity is required. Our slitting lines are suitable for processing materials up to with 2200 mm wide and thicknesses that vary from 0.2 to 20 mm, and stand out for the precision and quality of the finished product.
Our production range includes:
- slitting lines for light gauge
- slitting lines for medium gauge
- slitting lines for heavy gauge
- coil packing lines
Our slitting lines can process different materials, such as:
- cold or hot rolled steel
- galvanised steel, pre-painted
- high strength steel
- stainless steel
- aluminium
- copper
- zinc
- alloys
We pay great attention to the functionality and practicality of the equipment, in order to minimise the line set-up time.
Depending on the type of longitudinal slitting line, we can offer:
- automatic coil loading
- automatic coil head cutting sequence
- change of the slitter head – shuttle system – Automatic
- automatic circular blade changeover, with turnstile
- robotised automatic blade pack formation
- automatic blade locking
- scrap winder or scrap chopper
- system with mobile tensioning carriage
- strips tensioning with different systems depending on material type and surface
- quick changeover of felt and strip separating shafts
- automatic separators, with automatic disks positioning
- automatic strips end cutting
- movable clamping system to automatically bring the head of the strips in the recoiler clamp
- automatic coil unloading
- Integrated strapping system
All our slitting lines are equipped with software developed in our technical department. They allow for communication with the customer’s management programs, interconnection with automatic tool changing systems and with the coil packing line, if applicable. In addition, remote assistance is provided for line control and remote servicing.
Slitting line for metal coils
Slitting line for coils, metal coils. For widths of up to 2200 mm, thicknesses of up to 18 mm and speeds of up to 400 m/min. The lines are composed of high-precision slitters with quick tooling change for slitter, tensioning device and recoiler. Lines are offered with scrap ballers or scrap choppers. Moving tensioning devices with incorporated levelling. Lines are suitable to process materials used in the automotive and appliance industry, such as stainless steel, pre-painted, cold rolled steel, hot rolled carbon steel, electric steel, copper, brass and titanium.
Pressmach covers 3 Ranges of slitting lines
THIN GAUGE SLITTING LINE
Lines dedicated to small thicknesses at high speed.
TECHNICAL DATA
Coils | 10 ÷ 30 Tons |
Thickness | 0.2 ÷ 4 mm |
Width | 200 ÷ 2200 mm |
Speed | 200 ÷ 500 m/min |
MEDIUM GAUGE SLITTING LINES
Slitting Lines for high production.
TECHNICAL DATA
Coils | 15 ÷ 42 Tons |
Thickness | 0,5 ÷ 12mm |
Width | 500 ÷ 2200 mm |
Speed | 100 ÷ 200 m/min |
HEAVY GAUGE SLITTING LINES
Slitting lines for coils.
TECHNICAL DATA
Coils | 18÷ 60 Tons |
Thickness | 3 ÷ 18 mm |
Width | 800 ÷ 2200 mm |
Speed | 40 ÷ 100 m/min |
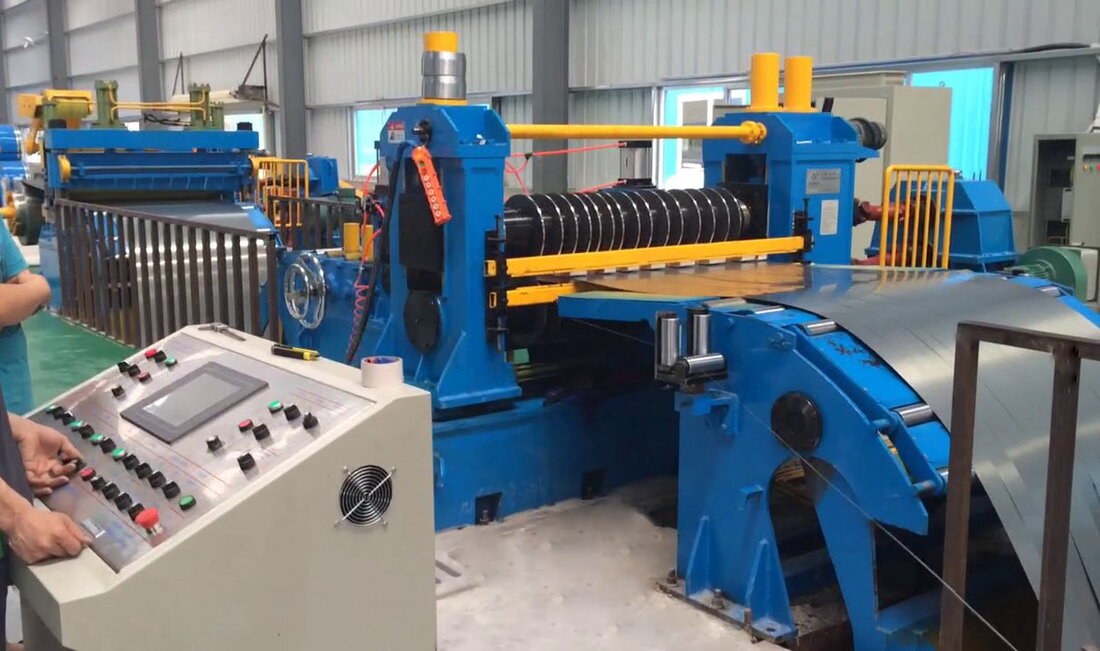
Slitting Lines
Working with Sheet Metal Coils
What is a Sheet Metal Coil Slitting Line?
The most basic explanation of what a metal coil slitting (or cutting line) does is, it take enormous rolls (or coils) of precisely created metal and creates smaller sheets and cut sections from the master coil. Sometimes these lines provide appearance treatments, and quality modifications for the metal.
Though the process may seem about as simple as unrolling a sheet of paper towels, there is a tremendous emphasis on accuracy and precision for each step of the sheet metal coil handling/slitting process.
The reason there is such precision required for this process is because final customers depend on receiving metal products from the line that meet tolerances often of .01 per inch or less. Additionally, the coatings which are applied during the metal slitting and unrolling process must also be very precise tolerances.
Components of a Metal Coil Slitting Line
The general layout of a sheet metal coil slitting line includes the following stations and processes:
#1 Coil handling equipment for loading metal coils onto and off of the various metal slitting and processing line.
Metal coils can weigh many tons depending on the type, gage, dimension and quality of metal being slit. Special lifts remove the metal coils from either tractor-trailers or railroad cars. They are then transported to the first stage of the metal coil line, the uncoiler, with the help of robotic coil handling carts or specially equipped lift trucks.
Once at the station for uncoiling, the coils can be hoisted into position on to a feeding capstan or directly into the coil processing machine with upenders, hoists, cranes, forklifts, and sometimes onto turnstiles for staging onto the uncoiler.
#2 The use of Uncoilers for unrolling the coil and controlling the speed of the metal coil into the slit processing line
The uncoiling machine is generally the first step of active coil processing on a metal coil slitting or processing line. It feeds the coil at carefully regulated and synchronized speed into the processing line, so that there are no deformations introduced unnecessarily by the uncoiling process.
Depending on the form of the line there may be a direct feed from the uncoiling machine into the levelers, tensioners, edge trimmers, even a portion of the uncoiled metal is allowed to run slack. This is to assist with line regulation and minimizing metal deformation.
#3 Different processing and shaping steps including levelers, feeders, edge trimmers, sheers, punch presses, peelers, straighteners, and notchers.
There are an almost limitless number of operations that can be performed on a metal slitting and cutting line. Some of these operations are designed to improve the accuracy of the final product, others are designed to improve the appearance, or characteristics of the metal for resisting corrosion and other factors.
Some of the processes for minimizing deformation and producing the most accurate slitting product, include cut to length, load leveling, tensioners, edge trimmers, in addition to presses and straighteners.
Other lines will add surface preparation such as pickling, acid baths, electroplating, galvanizing, and a variety of surface preparations.
#4 The recoiling equipment for those products that will be shipped in coil form, or sheet unloading equipment and stackers for products that will be sold in sheet or flat form.
The final product from a metal coil slitting line could either be smaller dimension coils, cut to length metal sheets, or possibly another coil that has been fully coated with a special surface preparation.
Each one of these steps that composes a metal coil slitting or cut to length line will also have multiple controls and often automation built in to ensure the high precision product required of the metals slitting and coiling industry.
By understanding the basic components that go into a sheet metal slitting and cutting line, it is easier to understand the factors that affect the performance as well as the cost of these industrial production facilities.
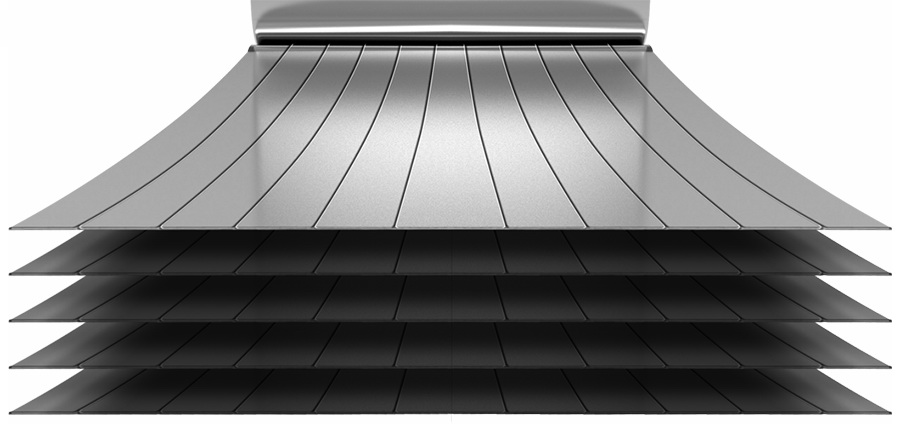